Leveraging the Potential of Biological Engineering
One exciting aspect of biological engineering is the potential to create products that can build the future. One example of this is being explored at the University of Nebraska, where a team of researchers is using bacteria and fermentation to produce bioplastics from corn. It’s an effort that could have potential applications in biomedical and industrial applications.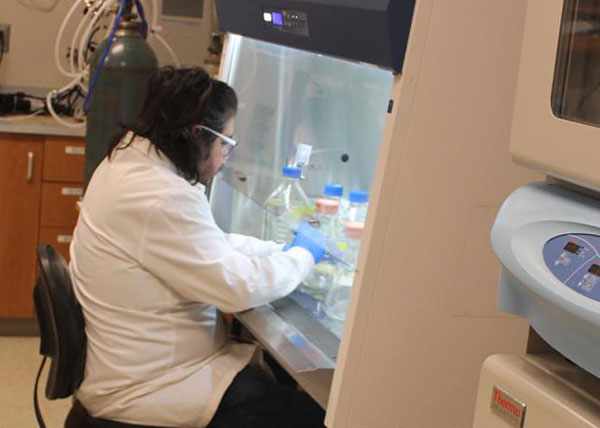
Corn to Plastic
Some biorefineries have a process to remove corn kernel fiber prior to the corn plant being used in the fermentation process for ethanol production, according to Elias Bamaca, Ph.D. candidate, University of Nebraska.
“Corn kernel fiber has a lot of carbohydrates, or sugars, in it and is mostly used as cattle feed,” Bamaca says. “Many companies are interested in adding value to that, and even if they sell some of their supply to a cattle feed company, they’ll still have extra corn kernel fiber.”
In addition, corn oil is extracted during the ethanol fermentation process and is sold as a fatty acid feed source for cattle. However, this type of corn oil is not to be confused with corn oil used for cooking, but it can be refined for human consumption through an expensive process. Instead, corn oil that’s not sold as cattle feed is sold for biodiesel production.
“Corn oil is interesting, because it has a lot of carbon, which acts as food for the bacteria,” Bamaca says. “However, after a certain amount, the bacteria stops growing. We have to add more sugar so the fermentation keeps giving good results.”
Getting Down to the Basic Level
All living things produce the naturally occurring biomolecule polyhydroxybutyrate (PHB), including humans, bacteria, and fungi. Bacteria produce PHBs to store energy—just as humans and animals store fat for energy. PHBs are simple molecules but can take the form of either short or long chains, depending on the conditions under which they’re produced. In addition to storing energy, PHBs have other functions, such as in cellular metabolism.
The polysaccharides in the corn kernel fiber must be broken down on a molecular level to access the basic sugars available in the fiber. According to Bamaca, there are different ways of breaking down the fiber, such as thermal treatment and using water at high pressure and temperature. Once those polysaccharides are broken down into smaller molecules, enzymes are added to extract the most basic sugars.
The enzymes Bamaca’s team selected were a lipase and a blend of cellulase-degrading enzymes produced by a bacteria. Adding the enzymes to the mixture improved the bioavailability of fatty acids.
During Bamaca’s research, which was done on behalf of the Nebraska Corn Board, the goal was to determine whether any of the biomaterial can be used as a value-added product. To start, Bamaca wanted to identify the bacteria that stored the most PHB. He found one that sometimes stores up to 90% PHB, which is a lot of bioplastic inside a bacteria.
“Not every bacteria uses sugar, but the one we selected uses both fatty acids and sugar,” says Bamaca. “We want to optimize the conditions because the bacteria needs to be stressed to produce the PHB.”
Fermentation: Bacteria Does the Work
The corn kernel fiber was then fermented in a shake incubator. The bacteria grows at 86°F and requires certain nutrients, so Bamaca and his team had to select the media in which they wanted to grow the bacteria. They tested different conditions to find the optimal mix, controlling for fermentation, agitation, and oxygen intake, first in shake flasks and later, in bioreactors.
Copper and boron are also added to the mix as part of the optimization process. These micronutrients are essential for the fermentation process to work, and the lipase require trace elements for communication and growth.
“The nice thing about fermentation is that the bacteria does the whole process for you,” Bamaca says. “The most exciting thing about this research is that Midwestern biorefineries producing ethanol already have this technology and it’s not a complicated process.”
Bamaca and his team believe that bioplastics can have valuable real-life applications, especially in the medical field. Because PHB is produced in the human body, the human body won’t reject them, so they can be a conduit for other medical processes.